Drug Substance Manufacturing
- Mabion offers clinical and commercial drug substance manufacturing of therapeutic proteins using mammalian and insect cell cultures, including biosimilars, innovative monoclonals, vaccine antigens and other recombinant proteins.
- We partner with clients throughout the world and offers high-quality, cGMP compliant manufacturing of biologic therapeutics in cleanroom grades D through A, at competitive price points.
- Based in the EU, our dedicated team of specialists understands that each molecule, whether a biosimilar or an originator, has its unique characteristics which require a customized approach to development, optimization and manufacture. The combination of our staff’s extensive experience and knowledge together with cutting edge technologies enables us to efficiently design and develop streamlined manufacturing processes, resulting in outstanding product yields and quality within mutually agreed project timelines.
- With our highly trained team and efficient planning, we can manufacture multiple batches utilizing a campaign mode to ensure maximum efficiency. In line with modern biopharmaceutical manufacturing practices, our state-of-the-art facility utilizes single-use technologies, ensuring that your product is free from contamination and minimizing switchover time between different products.
- Actively supporting the international efforts to reduce greenhouse gases emissions and increase sustainability, Mabion ensures that the achieved efficiency does not come at the expense of the environment. Thanks to our carefully designed waste management procedures we keep our ecological footprint at the lowest possible level.
Biosimilars
Due to the underlying objectives, development and manufacturing biosimilars is significantly different than innovators. Creating and producing a protein that is defined as “highly similar” to an existing therapeutic is in a certain way more challenging than developing and manufacturing an innovator, as it requires developing processes capable of manufacturing a product which will meet the pre-set specifications of the originator on all relevant key quality attributes. Therefore, many aspects of the development and manufacturing processes for a biosimilar are guided by the reference innovator product. Confirming similarity is a complex analytical task, which requires an advanced arsenal of equipment and robust analytical methods, all of which Mabion offers.
Mabion perfectly understands the challenges faced by biosimilar companies, as not long ago, we were one of them ourselves! Prior to the pandemic and transformation into a dedicated biologics CDMO, our company had a total of 6 biosimilars in the pipeline, at various stages of development. We went through all pre-clinical and clinical phases with our own products, building a strong expert team and gaining relevant experience which we now share with our clients. As of 2023, Mabion has fully transitioned to only focus on providing services to its clients without developing any internal products, thus eliminating any potential conflict of interest in prioritizing projects. For Mabion, our customers always come first.
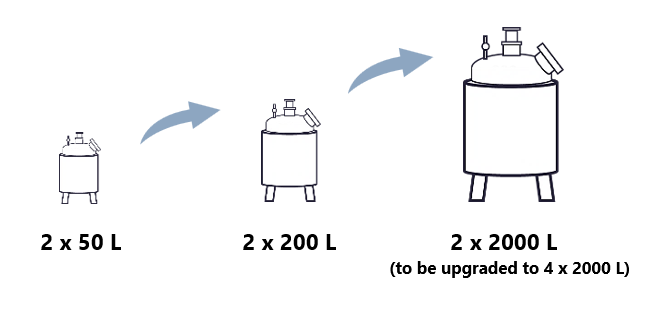
Mabion offers three sizes of bioreactors, which can be used in sequential manner as the product’s development advances.
Upstream processing
Upstream processing requires a high level of expertise and specialized equipment to ensure optimal cell growth and productivity. At Mabion, we have experience working with a variety of cell lines, including mammalian and insect lines dating back to our inception in 2007. The Inoculum stage cell cultures are performed in 50 to 5000 mL flasks, while bioreactor cultures are performed at 50 – 4000L scale (2 x 2000L). Mabion plans on adding two additional 2000L bioreactors, thus allowing for a pooled campaign of up to 8000L scale, or four separate 2000L batches.
Starting as a biosimilar developer, our company earned first-hand experience in planning, developing and running a large-scale manufacturing process for biosimilar products. We pride ourselves to be experts in manipulating cell culture conditions to obtain proteins with the exact desired characteristics – a skill of paramount importance, particularly at early-stage development of complex molecules. Our fit-for-purpose facility possesses all equipment necessary for end-to-end production of biosimilars, operated by well-qualified and experienced specialists. Furthermore, we possess extensive analytics in-house, which enables us to perform full DS/DP quality testing and reference drug characterization. Together, all these elements form a comprehensive manufacturing platform that can be utilized by a range of biosimilar companies, regardless of their size, product characteristics or development stage. Thanks to the breadth of available analytical methods and our problem-solving “can-do” attitude, we can either perform a seamless technology transfer, use the available process with or without additional adjustments or develop process de-novo, depending on the client’s needs.
Offering multiple technologies for cell culture (impellor driven stirred tank SUB or orbital shaken SUBs) and for cell harvest (single use depth filtration or single-use centrifugation) we can tailor the drug substance manufacturing process depending on the scale, product or process.
Our upstream processing offer comprises:
- 2 x 2000L stirred tank bioreactors (to be upgraded to 4 x 2000L stirred tank bioreactors) with a seed train consisting of 2 x 50L, 2 x 200L bioreactors and
- 2 x 2500L orbital shaking bioreactors with independent seed trains, which can be used in a stepwise manner to obtain large product quantities for clinical testing or commercial use
- Culturing mammalian and insect cell lines under tightly controlled conditions, with comprehensive in-line analysis of culture parameters, including physiological characteristics as well as gas and metabolite content, using state-of-the-art equipment
- Inoculum cell cultures in local A-class environments
- Point-of-use-preparation and storage of cell culture media and feeds
At Mabion, we specialize in the advanced manufacturing of biologics, leveraging extensive expertise alongside cutting-edge technologies. Our outstanding production capabilities span the entire drug substance manufacturing process, from cell culture to fill & finish, allowing us to consistently deliver high-quality products.
Downstream processing
Mabion is able to provide downstream processing for both innovative biologics as well as the more demanding biosimilars. Downstream processing is a crucial part of biosimilars manufacturing, requiring more stringent approach than for innovative biologics. Intensive analytical testing and process control during purification are of particular importance, as they help achieve sufficient consistency across batches. Matching impurities profile with the reference product can be also demanding and require adding additional purification steps.
Fine-tuning the biosimilar production process is a complex and demanding task that is best handled by a CDMO with deep expertise in this specialized field. Even extensive experience in manufacturing innovative biologics often falls short when it comes to navigating the unique challenges of biosimilars development and production, resulting in higher risks of a delayed market release and project cost overruns.
Biosimilars are the heart and soul of our company. Before transforming into a fully focused CDMO, we spent many years designing and optimizing the manufacturing processes for several of our own biosimilar candidates. We produced and supplied IMPs for Phase III clinical trials, performed across several European countries with participation of several hundred of patients. As of 2023, Mabion has transitioned to only focus on providing services to its clients without developing any internal products, thus eliminating any potential conflict of interest in prioritizing projects.
We offer a wide range of protein purification techniques. Our flexible downstream purification processes enable us to purify volumes from a single liter, all the way up to up to several thousand liters of active drug substance from a single batch. We have many years of experience working with both single-use and multi-use chromatographic systems, including affinity and ion-exchange chromatography in binding and non-binding modes. We provide a comprehensive range of chromatographic column sizes with customizable resin options. Importantly, our facility contains extensive and flexible DSP areas, which can accommodate even the largest columns. Complementing the chromatography steps, Mabion has extensive experience developing the right viral inactivation and filtration steps, completing our compliant and efficient viral contamination control strategy. Finally, in our post-viral filtration areas, we finalize the drug substance manufacturing process with a flexible ultra/diafiltration setup for concentration and buffer exchange into the formulation buffer and sterile filtration to ensure the absence of contaminants.
Should the desired process require it, Mabion has the capacity to prepare thousands of liters of buffers and solutions each day. We can prepare all necessary media and supplements for cell culturing in-house, providing our company with a significant advantage during the increasingly common logistical challenges. Nonetheless, we are also fully equipped for using ready-made buffers, feeds and media.
Following the completion of the drug substance manufacturing process, Mabion is equipped to store the produced active substances under refrigerated or frozen conditions, ensuring their stability and integrity. From here, we can proceed to the manufacture the drug product in house on our filling line (see page on our Fill & Finish services), or ship the frozen drug substance to a final storage or processing site of your choice.
Our downstream processing portfolio includes:
- Cell harvesting and separation from cells/culture medium via depth filtration and/or centrifugation
- Protein purification using various methods including: affinity chromatographies (e.g. protein A), ion-exchange chromatographies (incl. CEX and AEX), ultra/diafiltration as well as nanofiltration and sterile filtration.
- Virus inactivation and filtration
- Buffer exchange and formulation into the final drug product
- Preparation and storage of buffers
- Storage of the prepared drug substance
One of our key strengths lies in our fully integrated operations, where every step of the manufacturing process and quality control is conducted under one roof. Our state-of-the-art analytical unit, equipped with a comprehensive suit of analytical methods essential for biosimilars production, allows us to quickly obtain a full picture into what is happening in the bioreactor and later during the consecutive purification steps. This integrated approach translates into faster release times and higher cost-efficiency, making our platform both reliable and competitive.
Process validation and documentation
Modern process validation is a data-driven lifecycle approach, where validation activities are conducted throughout the product’s lifecycle. For this reason, our comprehensive panel of validation services spans from the earliest development stages to large-scale commercial production.
Mabion’s process validation and documentation offer includes:
- Design and preliminary evaluation of the drug substance manufacturing process
- Risk assessment and process control strategy development
- Process Performance Qualification (PPQ)
- Ongoing Process Verification through regular testing, analysis, and review of the manufacturing process data
- Revalidation following the introduction of changes to the manufacturing processes
- Comprehensive process validation documentation in line with relevant guidelines and requirements; including preparation of risk assessment, Process control strategy, Validation Master Plans (VMP, PVMP), Validation Protocols and Reports, Ongoing Process Verification Plan.
With Mabion, you can rest assured that every aspect of process validation is meticulously managed to ensure consistent quality and compliance.
Logistics and supply
Mabion’s capabilities are not limited to the manufacturing of drug substance and drug product. After completion of the drug product process or comprehensive sterile drug product fill and finish services, Mabion offers labelling and packaging services compliance to applicable EU regulations (link to Fill & Finish services). The finished products can be securely stored in our warehouses under a wide range of temperature conditions until they are ready for shipment. These services complete the entire manufacturing process, but Mabion’s services extend even beyond this. We are proud to offer additional services in areas such as quality control, preclinical and clinical analytics or regulatory affairs consultation.
Our clients also benefit from our well-equipped Logistics Unit with its own specialized fleet of vehicles. Mabion provides professional transportation services for pharmaceutical products under environmentally controlled conditions, eliminating the need to engage additional logistics companies. We can distribute drug product to nearly every location within Europe, inside and outside of the EU. With many years of experience in clinical trial logistics, we have successfully shipped thousands of IMPs and over 25,000 lab samples across 11 countries. This expertise enables us to seamlessly coordinate the transportation of biopharmaceutical products and related materials for Phase I-III multinational and multicenter trials.
Unlike most CDMOs, Mabion has its own logistics unit, capable of transporting your drug product, drug substance or samples to nearly every European country. Our experience includes shipping thousands of IMPs and over 25,000 lab samples across 11 countries. By choosing Mabion, you receive a true end-to-end CDMO service, starting from developing the upstream process to manufacturing the drug product and delivering it to the desired location.
Innovative antibodies (Mono- and Multi-specific)
Monoclonal antibodies have rapidly evolved from first-generation therapies into cutting-edge biologics, driving breakthroughs in the treatment of a wide range of diseases. The rise of bispecific and multi-specific antibodies represents another leap forward, enabling the targeting of multiple pathways or antigens with a single therapeutic molecule. These next-generation mAbs hold immense potential but require sophisticated development and manufacturing processes to achieve their full potential. For early-stage biotech companies developing new innovative mAbs, partnering with an experienced and versatile CDMO is essential in navigating the intricate challenges associated with drug originators.
At Mabion, we are committed in supporting pioneering biotech companies in developing and manufacturing both traditional and multi-targeted mAbs. With our state-of-the-art technology and deep optimization expertise, we help you to overcome challenges associated with expression, purification and other steps of the mAb production process, while maintaining high yields and most importantly, quality. Seamless integration of our upstream, downstream, and analytical processes as well as a full spectrum of complementary capabilities, such as regulatory support and logistics, translates into shorter timelines and cost-effective solutions, giving your program a competitive edge.
Partner with us to unlock the full potential of your monoclonal antibody candidates. From early-stage development to market readiness, Mabion is committed to delivering excellence every step of the way.
With Mabion as your partner, you can focus on advancing your science, confident that your manufacturing needs are in expert hands. With our partnership approach and a “can-do” attitude, we can transform your innovative ideas into impactful therapies.
Upstream processing
Upstream processing requires a high level of expertise and specialized equipment to ensure optimal cell growth and productivity. At Mabion, we have vast experience in working with a variety of cell lines, including mammalian and insect ones. Inoculum stage cell cultures are performed in 50 to 5000 mL flasks, while bioreactor cultures are performed at 50 – 4000L scale (2 x 2000L). Mabion plans on adding two additional 2000L bioreactors, thus allowing for a pooled campaign of up to 8000L scale, or four separate 2000L batches.
We carry out the process of cell separation after culturing from the remaining post-culture fluid or cell membrane, tailored to the preferred technology of our clients.
Our upstream processing offer comprises:
1. Cell line development and optimization
- Development of mammalian and insect cell lines for the purpose of monoclonal antibody production. Our in-house experts focus on developing robust, high-performance cell lines tailored to your unique requirements.
- Cell lines are optimized to achieve optimal yields and desired product characteristics.
2. Media development and optimization
- Development of customized media and feed strategies to enhance cell growth, productivity, and product quality, while minimizing variability and optimizing the Cost of Goods (COGs).
- Point-of-use-preparation and storage of cell culture media and feeds.
3. Bioreactor operations
- 2 x 2000L stirred tank bioreactors (to be upgraded to 4 x 2000L stirred tank bioreactors) with a seed train consisting of 2 x 50L and 2 x 200L bioreactors that allows for smooth transition from lab-scale to large-scale drug substance manufacturing.
- 2 x 2500L orbital shaking bioreactors with independent seed trains, which can be used in a stepwise manner to obtain large product quantities for clinical testing or commercial use.
- Inoculum cell cultures in local A-class environments.
- Real-time monitoring and control systems ensure consistent process performance and quality.
Downstream processing
Downstream processing is a crucial part of any biologics manufacturing activity. Intensive analytical testing and process control during purification are of particular importance, as they ensure consistency across batches with regards to meeting the critical quality attributes.
We offer a wide range of protein purification techniques. Our flexible downstream purification processes enable us to purify volumes from a single liter, all the way up to up to several thousand liters of active drug substance from a single batch. We have many years of experience working with both single-use and multi-use chromatographic systems, including affinity and ion-exchange chromatography in binding and non-binding modes. We provide a comprehensive range of chromatographic column sizes with customizable resin options. Importantly, our facility contains extensive and flexible DSP areas, which can accommodate even the largest columns. Complementing the chromatography steps, Mabion has extensive experience developing the right viral inactivation and filtration steps, completing our compliant and efficient viral contamination control strategy. Finally, in our post-viral filtration areas, we finalize the drug substance manufacturing process with a flexible ultra/diafiltration setup for concentration and buffer exchange into the formulation buffer and sterile filtration to ensure the absence of contaminants.
Should the desired process require it, Mabion has the capacity to prepare thousands of liters of buffers and solutions each day. We can prepare all necessary media and supplements for cell culturing in-house, providing our company with a significant advantage during the increasingly common logistical challenges. Nonetheless, we are also fully equipped for using ready-made buffers, feeds and media.
Following the completion of the drug substance manufacturing process, Mabion is equipped to store the produced active substances under refrigerated or frozen conditions, ensuring their stability and integrity. From here, we can proceed to the manufacture the drug product in house on our filling line, or ship the frozen drug substance to a final storage or processing site of your choice.
Our downstream processing portfolio includes:
1. Primary recovery
- Cell harvesting and separation from cells/culture medium via depth filtration and/or centrifugation
2. Protein purification and filtration
- Protein purification using various methods including:
- Affinity chroatographies (incl. protein A)
- Ion-exchange chromatographies (incl. CEX and AEX)
- Ultra/diafiltration
- Nanofiltration and sterile filtration
3. Virus inactivation
- Viral inactivation following filtration and chromatographic purification, both for early- and late-stage projects.
- Custom formulation solutions designed to stabilize your protein during storage
4. Preparation and storage of buffers
- Preparation of optimal buffers to enhance recovery and yield of target proteins
5. Storage of the drug substance
- Storage of the prepared drug substance under controlled conditions, prior to further processing
One of our key strengths lies in our fully integrated operations, where every step of the manufacturing process and quality control is conducted under one roof. Our state-of-the-art analytical unit, equipped with a comprehensive suite of analytical methods essential for biosimilars production, allows us to quickly obtain a full picture into what is happening in the bioreactor and later during the consecutive purification steps. This integrated approach translates into faster release times and high cost-efficiency, making our platform both reliable and competitive.
Process validation and documentation
Process validation is a regulatory requirement for the manufacturing of commercial products and a critical step in the manufacturing of biological medicinal products, ensuring that products consistently meet predefined quality attributes. Both EMA and FDA emphasize the importance of process validation as part of the regulatory framework governing the approval and ongoing monitoring of biological medicinal products. These two renown agencies have adopted a harmonized approach to process validation, emphasizing a lifecycle approach that incorporates risk-based principles.
Due to the complex nature of biological products, the drug substance manufacturing process itself significantly impacts product quality, safety, and efficacy. Thus, understanding and controlling the manufacturing process is essential in ensuring that the biological product consistently meets its intended quality attributes.
With Mabion, you can rest assured that every aspect of the process validation is meticulously managed to ensure consistent quality and compliance.
Modern process validation is a data-driven lifecycle approach, where validation activities are conducted throughout the product’s lifecycle, from development through commercial production. During the early stages of product development, we gain an in-depth understanding of the forthcoming manufacturing process through process characterization studies which lead us to identify critical quality attributes (“CQAs”) and critical process parameters (“CPPs”). This knowledge forms the basis for process design and development. Comprehensive process characterization is one of the foundations necessary for a successful process performance qualification (“PPQ”) and commercial production (LINK). The validation process continues through process qualification, where we demonstrate that the process delivers consistent results under commercial-scale batch manufacturing conditions. This includes complete validation of all analytical methods, qualification of equipment and facilities, validation of all critical raw materials, as well as PPQ to demonstrate that the process operates within the limits established during the process characterization studies. For PPQ studies, Mabion uses a 3+1 batches approach to ensure its successful completion. Finally, ongoing process verification ensures that the process remains in full control during routine production. Medical agencies expect manufacturers to use this data to ensure that the process is fully controlled and continues to produce products that meet specifications.
Our comprehensive panel of services covers whole lifecycle of process validation:
1. Design and preliminary evaluation of manufacturing process
- The foundation of a successful biologics manufacturing process lies in its initial design and evaluation. Our process design and preliminary evaluation services focus on defining a manufacturing process that is not only scalable and efficient but also capable of delivering a biologic product that consistently meets quality and regulatory standards.
2. Risk assessment and process control strategy development
- Risk assessment is a critical component of process validation, focusing on identifying and mitigating potential risks that could impact product quality, safety, or efficacy. Systematic risk assessment and control strategy development services provided by Mabion ensure that your process is robust and compliant with industry standards.
3. Process performance qualification
- We design and execute a comprehensive Process Performance Qualification (PPQ) plan, performing qualification runs under commercial-scale conditions. These runs validate the repeatability and robustness of the process. Key process parameters are monitored closely to confirm that the process delivers consistent quality across multiple batches.
4. Ongoing verification via testing and manufacturing process review
- After the PPQ phase, we implement a continuous monitoring program to ensure the process remains in a state of control. Our Ongoing Process Verification (OPV) services include regular testing, analysis, and review of critical manufacturing data. We use statistical process control (“SPC”) tools to detect trends, shifts, or out-of-specification results early, allowing for proactive interventions.
5. Revalidation after introducing process changes
- Process revalidation is essential whenever significant changes are made to the manufacturing process, equipment, or materials. Our revalidation services ensure that these changes do not adversely impact product quality, safety, or efficacy.
6. Comprehensive process validation documentation
- Comprehensive and accurate documentation is critical to ensuring regulatory approval and maintaining a state of control throughout the product lifecycle. Our documentation services encompass all aspects of process validation, ensuring full compliance with relevant guidelines and requirements: preparation of risk assessment, Process control strategy, Validation Master Plans (VMP, PVMP), Validation Protocols and Reports, Ongoing Process Verification Plan.
Partnership with Mabion ensures that your products are handled with the utmost care and precision from manufacturing to delivery, supporting the success of your clinical trials and commercial endeavors.
Logistics and supply
Mabion’s capabilities are not limited to the manufacturing of drug substance and drug product. After completion of the drug product process or comprehensive sterile drug product fill and finish services, Mabion offers labelling and packaging services compliance to applicable EU regulations. The finished products can be securely stored in our warehouses under a wide range of temperature conditions until they are ready for shipment. These services complete the entire manufacturing process, but Mabion’s services extend even beyond this. We are proud to offer additional services in areas such as quality control, preclinical and clinical analytics, and regulatory affairs consulting.
Our clients also benefit from our well-equipped Logistics Unit with its own specialized fleet of vehicles. Mabion provides professional transportation services for pharmaceutical products under environmentally controlled conditions, eliminating the need to engage additional logistics companies. We can distribute drug product to nearly every location within Europe, inside and outside of the EU. With many years of experience in clinical trial logistics, we have successfully shipped thousands of Investigational Medicinal Products (IMPs) and over 25,000 lab samples across 11 countries. This expertise enables us to seamlessly coordinate the transportation of biopharmaceutical products and related materials for Phase I-III multinational and multicenter trials. Logistics is a critical aspect of drug substance manufacturing, ensuring that your therapeutic protein is safely stored and delivered on time. Being a true end-to-end CDMO, we offer logistics support to streamline your supply chain from production to final delivery.
Mabion offers a true end-to-end service, ensuring our clients can focus on their core activities. Mabion, unlike most other CDMOs, has its own logistics unit, capable of transporting your drug product, drug substance or samples to nearly every European country, inside and outside the EU.
1. Storage under controlled conditions
- The foundation of a successful biologics manufacturing process lies in its initial design and evaluation. Our process design and preliminary evaluation services focus on defining a manufacturing process that is not only scalable and efficient but also capable of delivering a biologic product that consistently meets quality and regulatory standards.
2. Risk assessment and process control strategy development
- Risk assessment is a critical component of process validation, focusing on identifying and mitigating potential risks that could impact product quality, safety, or efficacy. Systematic risk assessment and control strategy development services provided by Mabion ensure that your process is robust and compliant with industry standards.
3. Process performance qualification
- We design and execute a comprehensive PPQ plan, performing qualification runs under commercial-scale conditions. These runs validate the repeatability and robustness of the process. Key process parameters are monitored closely to confirm that the process delivers consistent quality across multiple batches.
Other therapeutic proteins
Our CDMO offers comprehensive, cGMP-compliant drug substance manufacturing services for many different types of therapeutic proteins, including recombinant vaccine antigens, fusion proteins, enzymes, and other recombinant proteins. We provide end-to-end solutions, from cell line development and upstream processing to downstream purification, process validation, and logistics. With a focus on quality, flexibility, and regulatory compliance, we help bring your therapeutic protein from bench to market with precision and efficiency.
As the biopharmaceutical industry advances, the demand for high-quality therapeutic proteins continues to grow. These complex molecules require specialized expertise and technologies to ensure robust production, consistency, and compliance with stringent regulatory standards. At Mabion, we are committed in supporting your drug development journey with tailored manufacturing solutions that address the unique challenges of therapeutic protein production. Whether you need a reliable partner for clinical trial materials or commercial-scale production, we offer scalable, cost-effective manufacturing services designed to meet your specific needs.
At Mabion we specialize in the advanced drug substance manufacturing of enzymes and therapeutic proteins, leveraging extensive expertise alongside cutting-edge technologies. Our outstanding production capabilities span the entire manufacturing process, from cell culture to fill & finish, allowing us to consistently deliver high-quality biological medicinal products.
We offer the following manufacturing services:
- Upstream processing
- Dostream processing
- Process validation and documentation
- Logistics and supply
Recombinant vaccine antigens
Recombinant protein vaccines represent a critical class of vaccines designed to elicit a targeted immune response while offering improved safety profiles compared to other vaccine platforms. These protein based vaccines require complex manufacturing processes that demand expertise, precision, and compliance with stringent regulatory standards.
Our CDMO excels in providing advanced manufacturing services for protein vaccine antigens, providing comprehensive support at every stage of the lifecycle, from early-stage development to full-scale commercial production. With expertise experience in upstream and downstream processing, stringent process validation, and seamless logistics management, we deliver high-quality recombinant antigens for a broad range of vaccine applications. Our services are tailored to ensure that your product consistently meets regulatory requirements while maintaining efficacy, safety, and stability.
Our expert team recognizes that each vaccine, regardless of type, presents unique challenges and requires a customized manufacturing approach. By leveraging our extensive knowledge and state-of-the-art technology, we optimize every step of the production process to achieve exceptional results both in terms of timelines and product yield.
At Mabion, we are committed to delivering high-quality vaccine antigen manufacturing services that meet the specific needs of our clients while upholding the highest standards of safety and quality. Our dedication to continuous improvement and innovation positions us as a trusted partner in the biopharmaceutical industry.
Mabion’s experience includes a multi-year contract with Novavax involving various manufacturing and quality control services for Nuvaxovid – a protein-based COVID-19 vaccine produced in insect cell line Sf9 derived from Spodoptera frugiperda. Our team accomplished 100% successful engineering and transfer batches, and started GMP production of SARS-CoV-2 spike antigen DS in 2,500L scale. This outstanding batch success rate and perfect schedule adherence per value stream and production suite were assessed on 100% in the KPI analysis performed by Novavax.
We offer the following manufacturing services for vaccine antigens:
- Upstream processing
- Dostream processing
- Process validation and documentation
- Logistics and supply
“The addition of Mabion’s technical expertise and production capacity to Novavax’ global manufacturing network expands our ability to provide broad access to our vaccine across multiple regions, We look forward to building a long-term and mutually beneficial strategic partnership with Mabion.”